Manufacturing operations today are more complex than ever, requiring seamless coordination of machinery, labor, and materials. To achieve this, manufacturers rely on a powerful system known as Manufacturing Execution System (MES). But what is MES in manufacturing, and why is it so critical for modern manufacturers?
MES is the backbone of day-to-day production, bridging the gap between the shop floor and the top-floor systems. It provides real-time control and visibility into manufacturing processes, helping manufacturers ensure that production runs smoothly and efficiently. In this article, we’ll explore what MES is, how it works, and why it’s essential for achieving operational excellence in manufacturing.
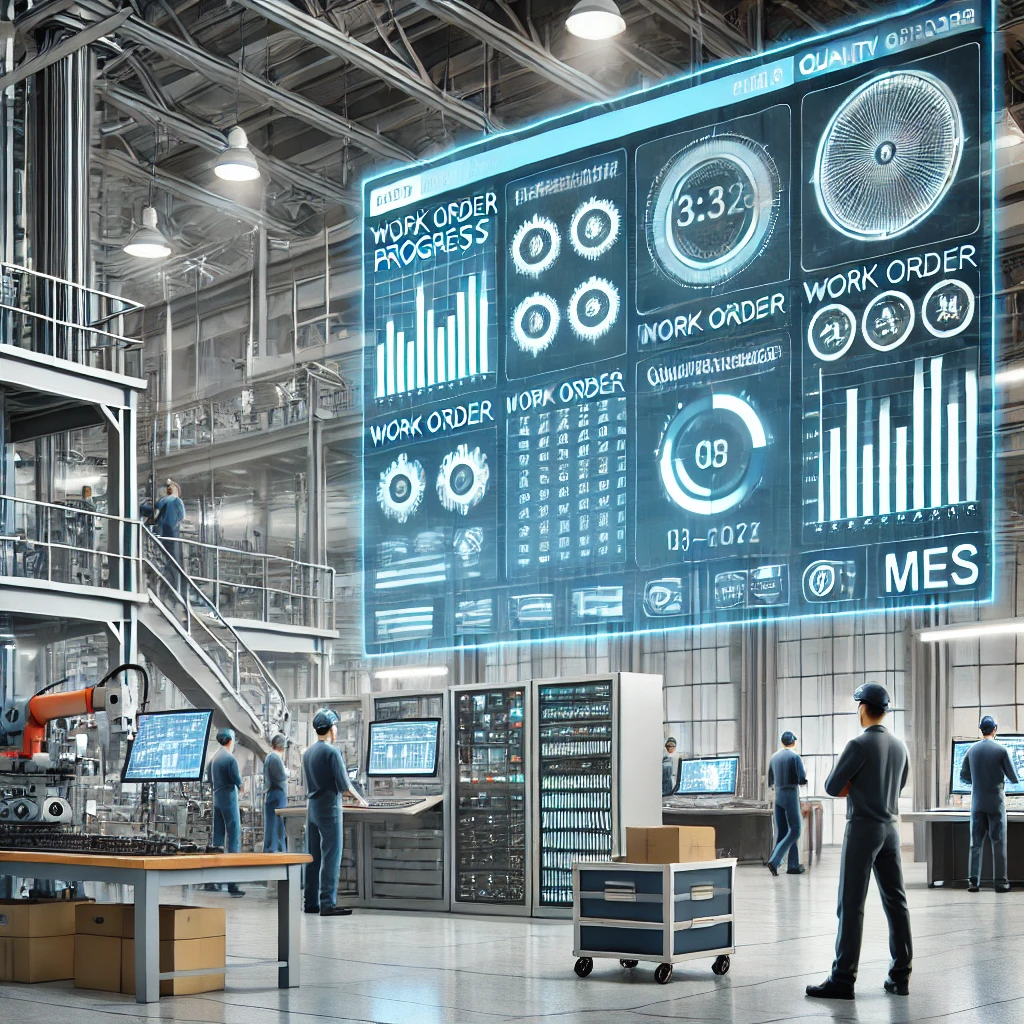
What is MES in Manufacturing?
A Manufacturing Execution System (MES) is a software solution designed to monitor, track, and control manufacturing operations in real-time. It serves as the link between the production floor and higher-level enterprise systems, such as Enterprise Resource Planning (ERP), by providing detailed insights into production processes, machinery performance, and resource utilization.
MES helps manufacturers manage everything from work orders and machine performance to quality control and production scheduling. By capturing real-time data from the shop floor, MES allows manufacturers to make informed decisions, optimize workflows, and improve overall efficiency.
At its core, MES is designed to:
- Monitor production as it happens.
- Track material flow through the factory.
- Ensure product quality by tracking key metrics.
- Optimize machine and labor efficiency.
Why MES is Critical for Manufacturers
Modern manufacturing involves managing multiple complex processes at once—everything from scheduling production jobs to ensuring that machines are running optimally. Without real-time insights, manufacturers risk falling behind due to bottlenecks, inefficiencies, and poor resource management.
Here’s why MES is critical for manufacturers:
1. Real-time Production Monitoring
With MES, manufacturers can track the progress of each production job in real time. This visibility allows managers to identify potential issues, such as bottlenecks or machine downtime, and resolve them quickly to keep production on schedule.
2. Optimized Resource Allocation
MES provides manufacturers with insights into how resources—such as labor, materials, and machinery—are being used. This helps optimize resource allocation, reduce waste, and ensure that production is running efficiently.
3. Enhanced Quality Control
Quality control is a key focus of MES. By tracking production data, MES allows manufacturers to monitor product quality at every stage of the process, ensuring that defects are caught early and corrective actions are taken immediately.
4. Improved Production Scheduling
MES integrates with production scheduling systems, helping manufacturers create optimized production plans. This ensures that materials are available when needed, machines are running at full capacity, and deadlines are met.
At Syncratech, we offer tailored MES solutions designed to help manufacturers achieve real-time visibility, improve efficiency, and ensure that production goals are met. Visit our homepage to learn more.
Key Features of MES in Manufacturing
When choosing an MES system for your manufacturing operations, it’s important to look for features that provide comprehensive control and visibility over your production processes. Here are some key features to consider:
1. Real-time Data Collection
MES collects data from machines, sensors, and production lines in real time, providing manufacturers with up-to-the-minute insights into how production is progressing.
2. Work Order Management
MES helps manufacturers manage work orders efficiently by tracking the status of each job and ensuring that resources are allocated properly.
3. Quality Control Integration
MES integrates with quality control systems, ensuring that products meet quality standards at every stage of production. This reduces the risk of defects and ensures that products are delivered to customers on time.
4. Machine Performance Monitoring
MES monitors the performance of machinery, helping manufacturers identify potential issues early and schedule preventive maintenance to reduce downtime.
5. Production Scheduling Integration
MES integrates with production scheduling systems, ensuring that production plans are followed and that resources are available when needed.
Benefits of Implementing MES in Manufacturing
Implementing MES in your manufacturing operations offers numerous benefits that can help improve efficiency, reduce costs, and ensure high-quality production:
1. Increased Productivity
By providing real-time insights into production processes, MES helps manufacturers identify inefficiencies and bottlenecks, allowing them to optimize workflows and increase productivity.
2. Reduced Downtime
MES helps manufacturers monitor machine performance and schedule preventive maintenance, reducing the risk of unexpected breakdowns and minimizing downtime.
3. Improved Resource Utilization
MES provides real-time data on resource usage, helping manufacturers allocate labor, materials, and machines more effectively. This leads to reduced waste and improved resource utilization.
4. Better Quality Control
By integrating quality control into the production process, MES ensures that products meet quality standards at every stage. This reduces defects, rework, and returns, leading to improved customer satisfaction.
How Syncratech’s MES Solutions Can Help Your Manufacturing Operations
At Syncratech, we understand the importance of having real-time visibility and control over your production processes. Our tailored MES solutions are designed to help manufacturers monitor production, optimize resource allocation, and ensure that products meet quality standards.
Here’s how our solution can benefit your business:
- Real-time production monitoring to track progress and identify potential bottlenecks.
- Work order management to ensure that jobs are completed on time and resources are used efficiently.
- Integrated quality control to catch defects early and ensure product quality.
- Machine performance monitoring to reduce downtime and improve operational efficiency.
- Production scheduling integration to ensure that production runs smoothly.
By implementing Syncratech’s MES solutions, manufacturers can improve efficiency, reduce costs, and ensure that production goals are met. Visit our homepage to learn more.
FAQs About MES in Manufacturing
1. What is MES in manufacturing?
A Manufacturing Execution System (MES) is software that tracks and monitors production processes in real time. It provides manufacturers with insights into resource usage, machine performance, and production progress, helping them optimize workflows and improve efficiency.
2. How does MES improve production efficiency?
MES improves production efficiency by providing real-time data on production processes, helping manufacturers identify bottlenecks, optimize resource allocation, and ensure that production runs smoothly.
3. Can MES systems integrate with ERP systems?
Yes, MES systems integrate with ERP systems to provide manufacturers with a unified view of their operations, from production to inventory and financial management.
4. How does MES help with quality control in manufacturing?
MES integrates quality control into the production process, tracking product quality at every stage and ensuring that defects are caught early. This helps reduce rework and improve product quality.
Final Thoughts
For manufacturers looking to optimize their operations and improve efficiency, implementing a Manufacturing Execution System (MES) is essential. By providing real-time visibility into production processes, MES helps manufacturers make data-driven decisions, reduce downtime, and ensure that products meet quality standards.
At Syncratech, we offer customized MES solutions designed to help manufacturers monitor production, improve efficiency, and ensure that production goals are met. To learn more about how our MES can benefit your business, visit our homepage today.