In today’s highly competitive manufacturing industry, cost control is crucial to maintaining profitability and staying ahead of the competition. For manufacturers, finding ways to reduce costs without sacrificing product quality or customer satisfaction is a constant challenge. Enterprise Resource Planning (ERP) systems provide manufacturers with the tools to streamline operations, optimize resources, and significantly reduce manufacturing costs.
In this article, we’ll explore how manufacturers can leverage ERP systems to cut costs and improve efficiency across their operations.
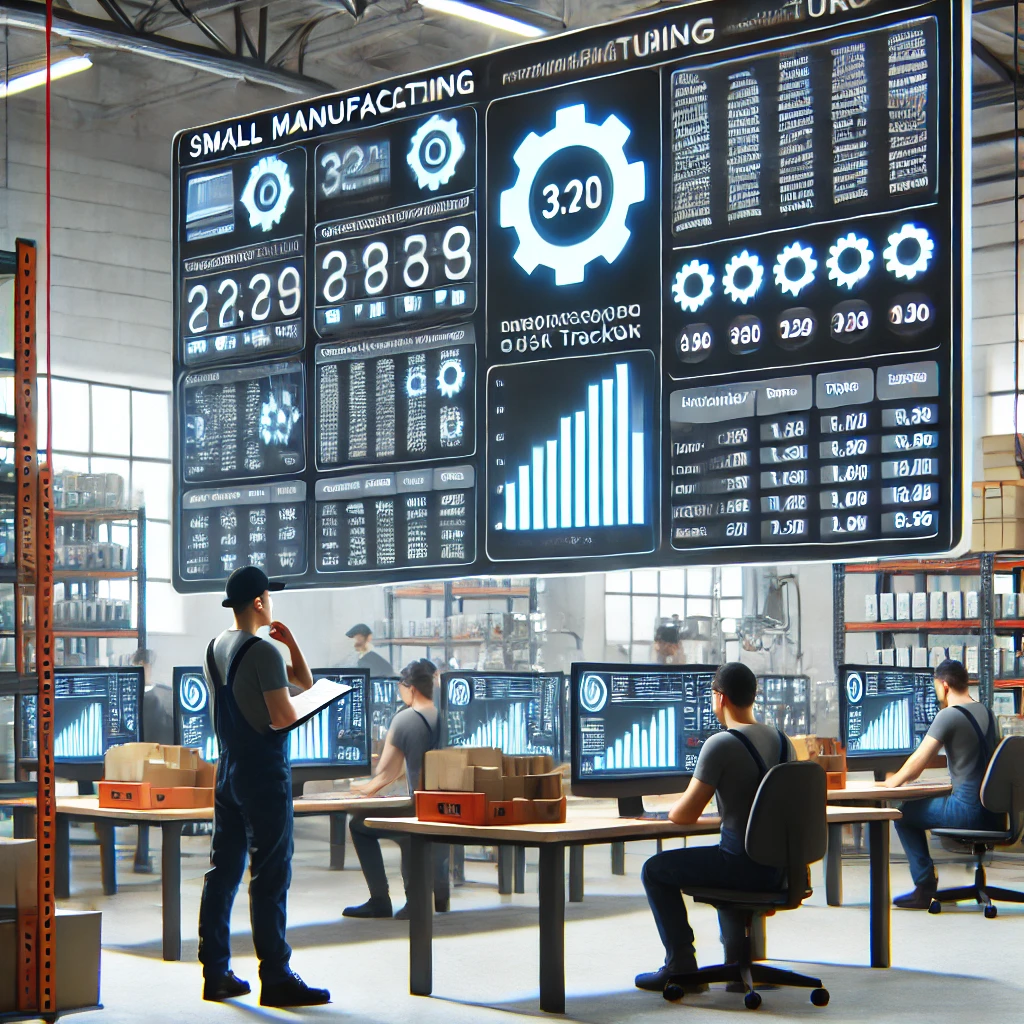
Why ERP Systems Are Essential for Reducing Manufacturing Costs
An ERP system integrates various functions within a manufacturing business—such as production planning, inventory management, procurement, and financials—into one centralized platform. This integration allows manufacturers to gain real-time visibility into their operations and make informed decisions that improve efficiency and reduce costs.
Here’s why ERP systems are critical for cost reduction in manufacturing:
1. Improved Resource Utilization
ERP systems provide manufacturers with real-time data on inventory, labor, and machinery. This helps optimize resource allocation, reducing waste and ensuring that materials and labor are used efficiently.
2. Streamlined Production Processes
With ERP systems, manufacturers can automate and streamline production processes, eliminating manual tasks that lead to delays and errors. This reduces production time, minimizes bottlenecks, and lowers operational costs.
3. Better Financial Control
ERP systems provide manufacturers with real-time insights into production costs, revenues, and profits. By monitoring financial data closely, manufacturers can identify areas where costs can be reduced and make adjustments to stay within budget.
4. Reduced Waste and Overproduction
ERP systems help manufacturers track material usage and production output in real time. This reduces the risk of overproduction, which ties up capital in unsold goods, and helps minimize waste, leading to lower production costs.
Key Ways ERP Systems Reduce Manufacturing Costs
Let’s dive deeper into the specific ways ERP systems help manufacturers cut costs:
1. Optimized Inventory Management
Excess inventory ties up capital and increases storage costs. ERP systems offer real-time visibility into inventory levels, helping manufacturers manage stock more effectively. By automating reordering and preventing overstocking, ERP systems reduce inventory costs and ensure that materials are available when needed.
2. Reduced Labor Costs
By automating repetitive tasks such as production scheduling, material tracking, and data entry, ERP systems reduce the need for manual labor. This not only reduces labor costs but also frees up employees to focus on more value-added tasks, improving overall productivity.
3. Efficient Production Scheduling
ERP systems enable manufacturers to create optimized production schedules based on real-time data. This ensures that resources such as labor, materials, and machinery are allocated effectively, reducing downtime and improving production efficiency.
4. Lower Maintenance Costs
ERP systems track machine performance and schedule preventive maintenance, reducing the risk of unexpected breakdowns. By keeping equipment running smoothly, manufacturers can minimize costly downtime and repair expenses.
5. Accurate Financial Reporting
With detailed financial data at their fingertips, manufacturers can track expenses in real time and identify areas where savings can be made. ERP systems allow businesses to create more accurate budgets, monitor spending, and control costs more effectively.
How Syncratech’s ERP Solutions Can Help You Reduce Costs
At Syncratech, we understand the importance of controlling costs in manufacturing. Our tailored ERP solutions are designed to help manufacturers streamline their operations, improve efficiency, and reduce expenses.
Here’s how our ERP system can help your business:
- Optimize inventory levels to reduce excess stock and minimize carrying costs.
- Automate production scheduling to improve resource allocation and reduce labor costs.
- Track financial data in real time to control spending and manage budgets effectively.
- Schedule preventive maintenance to minimize equipment downtime and repair costs.
- Monitor material usage to reduce waste and avoid overproduction.
By implementing our ERP system, manufacturers can take control of their costs, improve efficiency, and enhance profitability. Visit our homepage to learn more about how we can support your cost-saving initiatives.
Benefits of Using ERP to Reduce Manufacturing Costs
Implementing an ERP system offers several benefits that can help manufacturers reduce costs and improve their bottom line:
1. Increased Productivity
By automating manual tasks and optimizing production schedules, ERP systems improve productivity, allowing manufacturers to produce more with the same resources.
2. Better Resource Allocation
ERP systems provide real-time data on labor, materials, and machinery, ensuring that resources are used efficiently and that waste is minimized.
3. Lower Operational Costs
With streamlined processes and improved resource management, manufacturers can reduce operational costs and increase profitability.
4. Improved Financial Control
ERP systems allow manufacturers to track costs, monitor budgets, and identify areas for savings, helping them maintain better financial control.
FAQs About Reducing Manufacturing Costs with ERP
1. How do ERP systems reduce labor costs in manufacturing?
ERP systems automate repetitive tasks, reducing the need for manual labor. This helps manufacturers lower labor costs and improve productivity by allowing employees to focus on higher-value activities.
2. Can ERP systems help reduce equipment downtime?
Yes, ERP systems track machine performance and schedule preventive maintenance, reducing the risk of unexpected breakdowns and minimizing downtime, which in turn lowers maintenance costs.
3. How do ERP systems optimize inventory management?
ERP systems provide real-time visibility into inventory levels and automate reordering processes. This helps manufacturers maintain optimal stock levels, reducing excess inventory and minimizing carrying costs.
4. How do ERP systems improve financial control in manufacturing?
ERP systems provide real-time data on production costs, revenues, and profits, helping manufacturers track expenses and manage budgets effectively. This improves financial control and helps manufacturers identify cost-saving opportunities.
Final Thoughts
Reducing manufacturing costs is essential to maintaining profitability and staying competitive. By implementing an ERP system, manufacturers can streamline operations, optimize resource allocation, and gain better financial control, leading to significant cost savings and improved efficiency.
At Syncratech, we offer customized ERP solutions that help manufacturers reduce costs and improve profitability. To learn more about how our ERP can help your business, visit our homepage today.